BMW ditches electric: Switches to hydrogen for its factory fleet
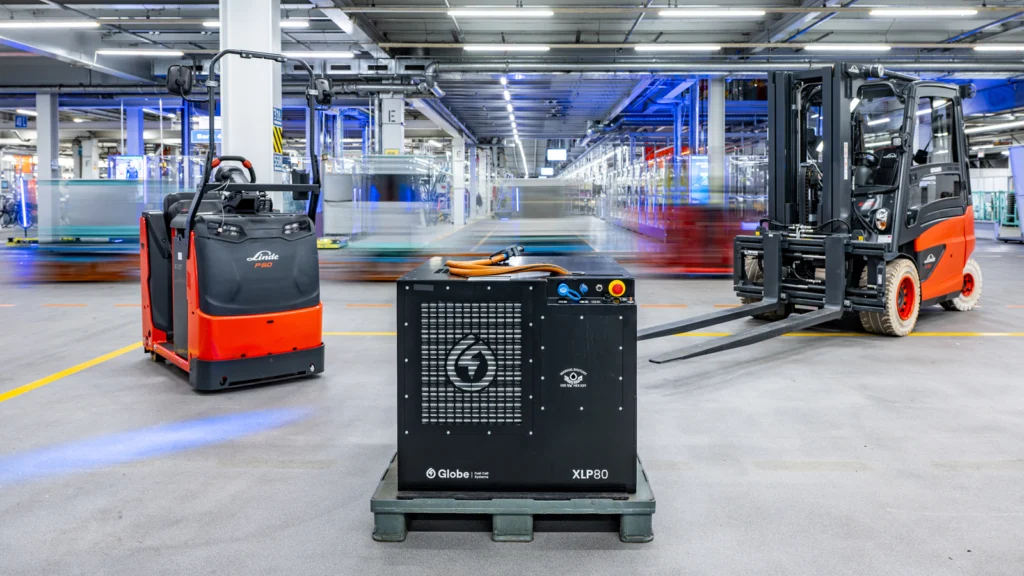
In the glamorous world of carmaking, forklifts and tugger trains don’t often make headlines. But at BMW’s Regensburg plant, these workhorses of production are undergoing a quiet revolution by ditching electric batteries for hydrogen.
By 2030, this cornerstone of BMW’s operations – producing a colossal 1,400 BMW X1 and X2 models every single day – will have transitioned its battery electric ‘intralogistics’ fleet to hydrogen propulsion.
A pragmatic move, designed to streamline operations whilst meeting the German powerhouse’s stringent sustainability goals.
BMW’s Regensburg plant
Opened in 1986, and winning “Factory of the Year” in 2024, Regensburg is one of BMW’s flagship production sites, rolling out SUVs destined for everywhere from Beverly Hills driveways to Munich high streets.
Behind every gleaming BMW X1 and X2, however, is a fleet of forklifts and tugger trains working tirelessly to keep the assembly line running day and night.
Currently, these ‘intralogistics’ vehicles rely on swappable battery packs – a system that gets the job done but comes with some challenges.
The batteries are large, cumbersome, and require manual replacement twice every shift. Each swap takes at least 15 minutes, involves cranes, and occupies valuable floor space for storage and equipment.
Not so good when every square inch of factory floor comes at a premium.
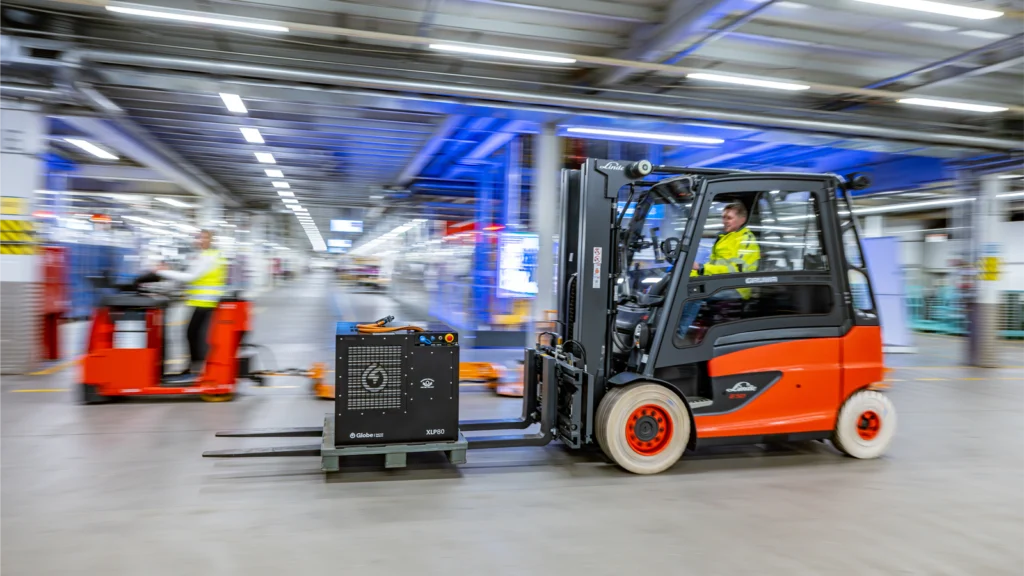
The hydrogen solution
Starting in 2026, BMW will begin rolling out hydrogen fuel cells to all 230 forklifts and tugger trains at Regensburg.
Hydrogen refuelling takes just a few minutes – comparable to filling up a conventional fuel tank – and eliminates the need for bulky battery-swapping infrastructure.
To support the transition, BMW is installing a two-kilometre hydrogen pipeline and six decentralised filling stations across the plant.
Delivered in trailers that double as storage, this system ensures a steady and efficient supply of hydrogen to keep operations running seamlessly.
Project Manager Katharina Radtke highlights the efficiency of the hydrogen system, saying:
“The advantage of hydrogen is that refuelling is very fast – just like with conventional fuels. The filling stations required for this will be installed directly within the different production areas and do not take up much space.”
“Once the conversion is completed, our annual hydrogen consumption will be around 150 tonnes,” says Radtke.
Plug-and-Play hydrogen fuel-cells from Globe
BMW’s new kit is powered by Globe’s innovative “XLP 80” system. Globe, a spin-off of Mercedes-Benz, has designed its modular hydrogen fuel cells to match the exact size and connectivity standards of the plant’s existing Linde battery packs.
This plug-and-play compatibility ensures a smooth, disruption-free transition.
Instead of forking out for new machinery, operators simply swap out the batteries *once* for a fuel-cell-in-a-box – then just refuel it in 5 minutes ready for the next shift.
The system offers consistent power delivery, outperforming conventional lead-acid batteries, which lose efficiency below a 50% charge.
Globe’s cells are built to meet the rigorous demands of automotive production, with an impressive operating lifespan of 20,000 hours.
And it’s not just about performance. Globe points out the environmental advantages of their hydrogen system:
“When operating a Globe XLP80 unit, only heat and water are produced as emissions. Harmful substances such as lead and sulphuric acid, which are produced by toxic batteries, are reduced to a minimum.”
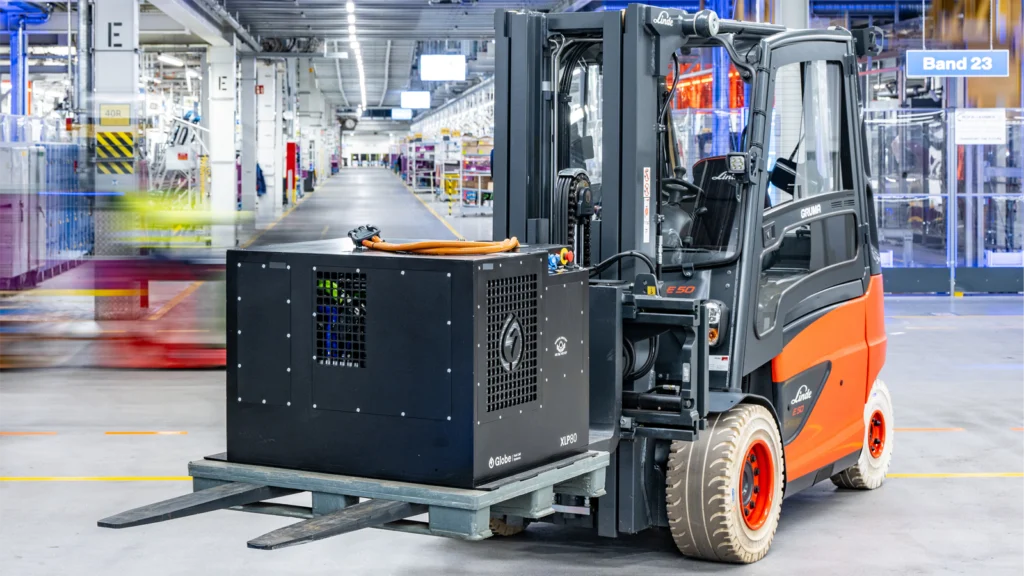
A blueprint for the future
Could Regensburg’s shift serve as a model for other automakers looking to enhance efficiency and reduce emissions in their logistics operations?
Hydrogen isn’t just staying behind the scenes at the German carmaker either.
BMW is preparing its Toyota-sourced hydrogen fuel-cell iX5 for series production in the next couple of years, proving that hydrogen’s applications extend beyond the factory gate, to the open road.