Germany pledges €5.1million for hydrogen engine research for farming and construction
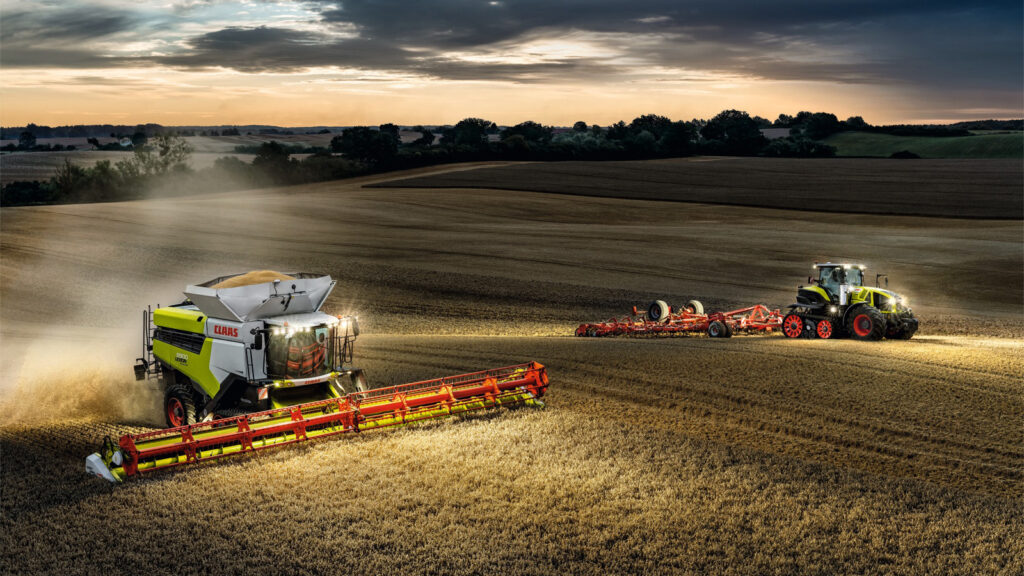
Germany’s Federal Ministry for Economic Affairs and Climate Action has put €5.1million on the table to fast-track hydrogen-powered drive systems for construction and agricultural machinery.
The three-year project pulls together a powerhouse team of industry leaders and research experts aiming to create durable, low-emission hydrogen internal combustion engines ready for the toughest tasks.
Who’s involved?
The project, known as “PoWer”, brings together some serious players.
Engine specialist DEUTZ, agricultural machinery giant Claas, and heavy-equipment maker Liebherr are leading the charge alongside cutting-edge researchers from the German Aerospace Center (DLR) and top universities.
Others including spark plug manufacturer NGK, exhaust systems maker Purem, and engine-oil maker Castrol will contribute advanced technical expertise.
MAHLE, another German firm, and one of the world’s leading automotive suppliers, is coordinating the whole thing, while TÜV Rheinland ensures the engines meet strict safety and performance benchmarks.
Dr. Marco Warth, Vice President Corporate Research and Advanced Engineering at MAHLE, said:
“At MAHLE, we have been working on the development of hydrogen engines for years and are delighted that we can now also contribute this expertise, together with strong partners, to the latest developments for the off-road sector.”
“Only the cooperation of such diverse partners and experts in the respective technologies enables a holistic approach and impressively shows the innovation potential of German research and industry in the mobility sector.”
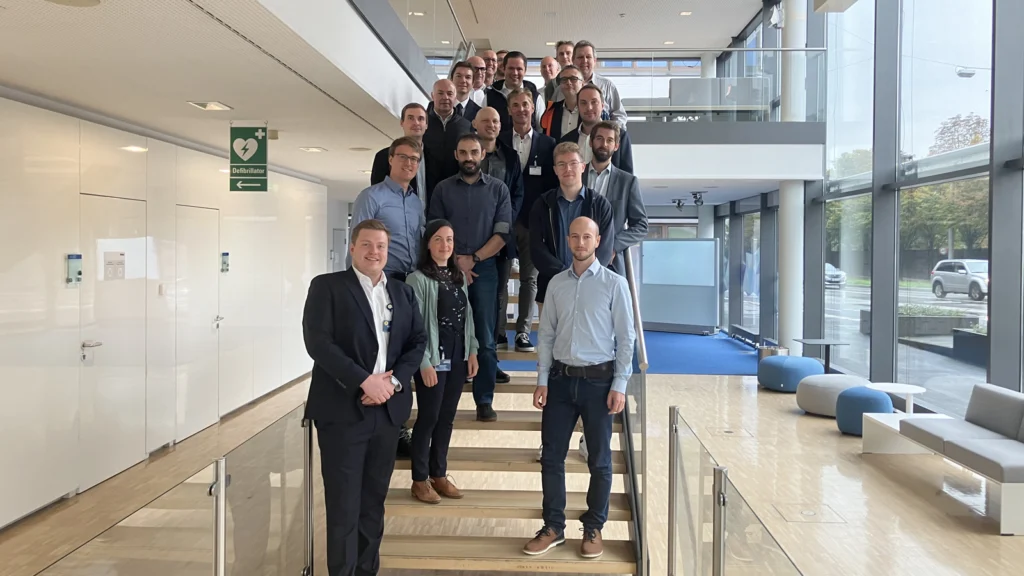
What’s the mission?
The consortium’s mission extends beyond just engine development, and into creating a hydrogen-powered ecosystem, including fuel supply, maintenance frameworks, and operational models tailored to off-road challenges.
Engineers will push the limits of hydrogen internal combustion engine technology, focusing on durability, operational efficiency, and near-zero emissions.
The project targets multiple engineering fronts, including advanced exhaust gas after-treatment systems designed to meet stringent future emissions regulations for non-road mobile machinery (NRMM).
Researchers will also develop friction-reducing technologies to extend engine life and improve fuel efficiency, along with hydrogen-compatible materials built to withstand extreme working conditions like dust, vibration, and continuous heavy loads.
Comprehensive testing will take place both in state-of-the-art labs and in real-world field trials.
These tests will measure emissions performance, fuel efficiency, and overall reliability under harsh operating conditions.
In parallel, system-level studies will explore how these hydrogen engines integrate into fleet operations and large-scale agricultural and construction infrastructures.
Why hydrogen internal combustion engines make sense
Hydrogen-powered engines pack a serious punch for heavy-duty work. They offer long operating times, rugged durability, and practically zero emissions – exactly what’s needed for demanding construction sites and farm fields where battery-only machines may struggle.
Unlike battery-electric powertrains that require frequent charging and may falter in remote locations, hydrogen engines can be refuelled quickly, minimising downtime.
Their compatibility with existing engine architectures also makes them a practical, scalable solution for industries already invested in internal combustion technology.
Hydrogen internal combustion engines may be less inflationary than battery electric alternatives or even hydrogen fuel cells, as they leverage established supply chains and existing well-established manufacturing infrastructure designed for petrol and diesel engines.
This reduces dependency on entirely new production systems, potentially keeping costs more stable over time.
What’s next?
By the end of the project, the consortium aims to have hydrogen-powered engines ready for deployment in demanding off-road environments such as construction sites and large-scale farming operations.
Beyond just technology development, the project aims to create a blueprint for integrating hydrogen engines into construction and agricultural operations at scale.
With successful development, the team hopes to position hydrogen-powered machinery as a durable, eco-friendly alternative that sets new standards for heavy-duty equipment.